In 2025, A4 thermal paper in Bangladesh has become a crucial item for businesses relying on thermal printers. Prices...
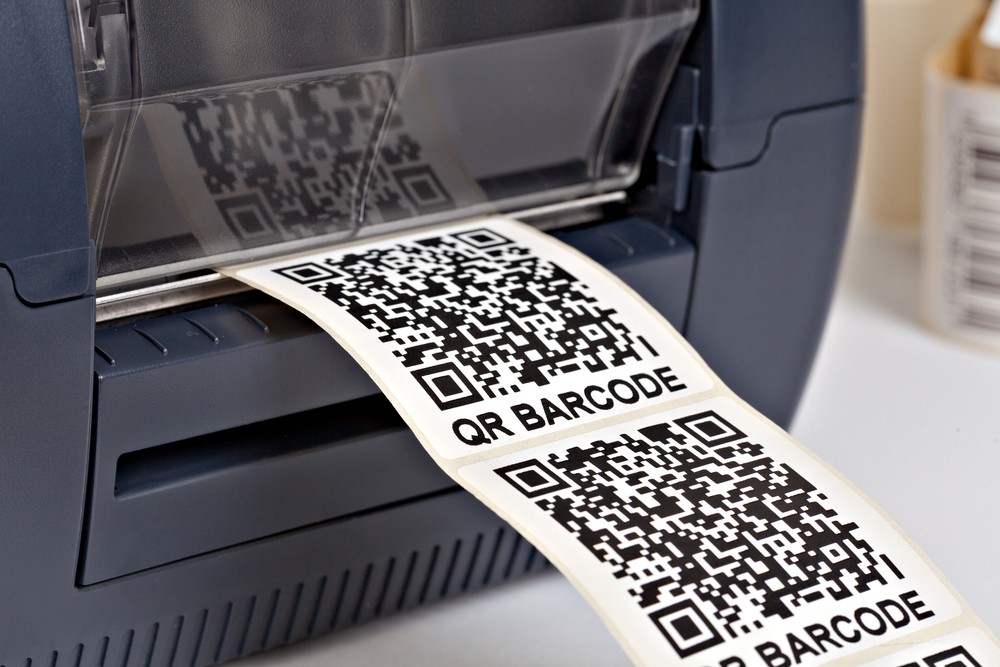
Barcode Label Print Issue - Print Not Coming Correct
Barcode label printing is an essential aspect of many businesses and industries, including retail, warehousing, healthcare, logistics, and manufacturing. However, sometimes, businesses experience issues when the print doesn't come out correctly. This issue, commonly known as "Barcode Label Print Issue," can significantly impact operations and lead to inefficiencies. The key to resolving these issues lies in understanding the various factors that contribute to the problem and exploring effective solutions.
Common Barcode Label Print Issues
When printing barcode labels, businesses often encounter a variety of problems, including blurry or missing barcodes, incorrect label alignment, distorted images, and poor quality prints. These issues can arise due to several factors that influence the quality of barcode printing.
Key Factors Affecting Barcode Label Printing
-
Printer Settings and Configuration
One of the primary causes of incorrect barcode label printing is improper printer settings or configuration. Printers often need to be calibrated for specific types of labels, such as size and material. When the printer’s settings are not correctly adjusted, it can result in poor quality prints, misalignment, or incorrect barcode sizes.
Solution: Ensure that the printer is set up for the specific label dimensions, media type, and barcode standard being used. Always check the printer manual for instructions on configuring the printer to match the specifications of the barcode labels. -
Label Material and Quality
The quality of the labels being used plays a significant role in the print output. Some labels, especially those made from low-quality materials, may absorb ink or adhesive in ways that result in distorted or blurry barcodes. If the material is not compatible with the printer or the ink type being used, it can lead to print issues.
Solution: Use high-quality labels that are designed for thermal or inkjet printing, depending on the type of printer being used. It's also essential to choose labels that match the printer’s specifications (e.g., thermal transfer or direct thermal labels). -
Printer Maintenance and Cleanliness
Over time, printers accumulate dust, debris, and ink residue, which can interfere with the printing process. Dirty printer heads or rollers can lead to poor print quality, such as faded or inconsistent barcode printing. This can result in barcodes that are unreadable by scanners, causing delays in processing or inventory management.
Solution: Regular maintenance of the printer, including cleaning the print head, rollers, and other parts, can significantly improve print quality. Ensure the printer is cleaned as part of a routine maintenance schedule to prevent these issues. -
Software and Driver Issues
The software used to design and print barcode labels can also contribute to printing problems. If there is an issue with the label design software, the print settings may not be correctly applied, leading to improperly sized or positioned barcodes. Similarly, outdated or incompatible printer drivers may cause print failures or incorrect outputs.
Solution: Always use the latest version of the software and printer drivers. Check for updates from the manufacturer and ensure the software settings align with your printer configuration. Correctly design labels to ensure barcode dimensions and placements are optimized. -
Resolution and Print Quality Settings
The resolution settings on the printer impact the sharpness of the print. Low-resolution settings may result in fuzzy or pixelated barcodes that are hard to scan. This issue is particularly common when printing at lower quality settings to save time or ink, especially when working with barcodes that require a high level of detail.
Solution: Set the printer resolution to the highest possible setting when printing barcode labels, especially if the barcode includes dense data. For optimal results, a resolution of at least 300 DPI (dots per inch) is recommended for clear and precise printing. -
Environmental Factors
Environmental conditions, such as temperature and humidity, can also affect the print quality. Extreme temperatures or high humidity can cause the ink to smudge or the labels to warp, resulting in improper barcode printing.
Solution: Store labels and printers in controlled environments, where the temperature and humidity levels are maintained within the recommended ranges. Ensure that the printer is used in an environment free from excessive dust or moisture. -
Incorrect Barcode Formatting
Barcode format errors are another common cause of print issues. When the wrong barcode type or format is used for a specific application, it can lead to issues with printing and scanning. For example, a barcode may be too small to scan or improperly sized for the label.
Solution: Use the correct barcode format for your specific application, whether it's Code 128, UPC, QR, or another type. Ensure that the barcode is sized appropriately for the label and follows the recommended guidelines for readability.
Troubleshooting and Resolving Barcode Print Issues
If you are experiencing issues with barcode label printing, there are several steps you can take to troubleshoot and resolve the problem.
-
Test Prints
Perform test prints to determine if the issue is related to the printer or the labels. Print a sample barcode and check it with a scanner. If it scans properly, the issue may lie with the label design or software. -
Printer Calibration
If the print is misaligned or distorted, recalibrate the printer. Many printers allow you to perform automatic calibration through their menu settings. -
Review Software Settings
Double-check the settings in your label design software. Ensure that the correct barcode format, dimensions, and alignment are being used. -
Check Barcode Readability
Use a barcode scanner to verify if the barcode is readable after printing. If the scanner cannot read it, consider adjusting the contrast, size, or resolution of the barcode. -
Consult Manufacturer Support
If troubleshooting does not resolve the issue, contact the printer or software manufacturer’s support team for assistance. They may offer guidance or firmware updates to resolve any known issues.
Conclusion
Barcode label print issues, such as incorrect or unclear printing, can be a significant challenge for businesses relying on barcode technology. However, by understanding the key factors that influence print quality—such as printer settings, label material, software, maintenance, and environmental conditions—businesses can troubleshoot and resolve these issues effectively. By implementing proper calibration, using high-quality materials, and following best practices, you can ensure accurate, reliable barcode printing that supports smooth operations and prevents costly delays.
Leave a comment